From idea to solution
Every empty bottle is a new opportunity – that's the motto behind Pumphead. What began as a pretty liqueur bottle is now a clever upcycling product: an attachment that transforms almost any glass bottle into a stylish soap dispenser in no time. But how exactly is a Pumphead made?
The idea: preserve beauty, add function
Pumphead founder David Brönnimann originally pursued a completely different career – as a medical masseur. But everything changed with the founding of his spirits brand Lewa spirits in 2019. His bottles were so well-received that many customers didn't want to simply throw them away. The solution: upcycling instead of recycling. And so the idea for Pumphead was born – out of a desire to meaningfully combine design and function.
The beginning: A product is created
In 2020, David took the bold step of developing a new product. The challenge was ambitious: The attachment had to fit as many bottles as possible—whether for soap, shower gel, or disinfectant. But the core component, the adapter, presented a particular challenge.
The procedure:
Precision through injection molding
The adapters are manufactured using an injection molding process , in which liquid material is pressed under high pressure into a customized metal mold.
This process guarantees consistent quality and durability – all while minimizing energy consumption. Nimoulda's workshop uses solar power not only for the machines but also to heat the production facilities.
The adapter: small but crucial
Together with Nimoulda AG in Täuffelen near Bern, David developed the perfect adapter – a small component with a big impact. It ensures that the cap closes and fits up to 99% of all common bottles. The path to this goal was anything but easy: The first prototype didn't stand up to practical testing. So, a new injection mold was developed – precisely manufactured using solar-powered machines.
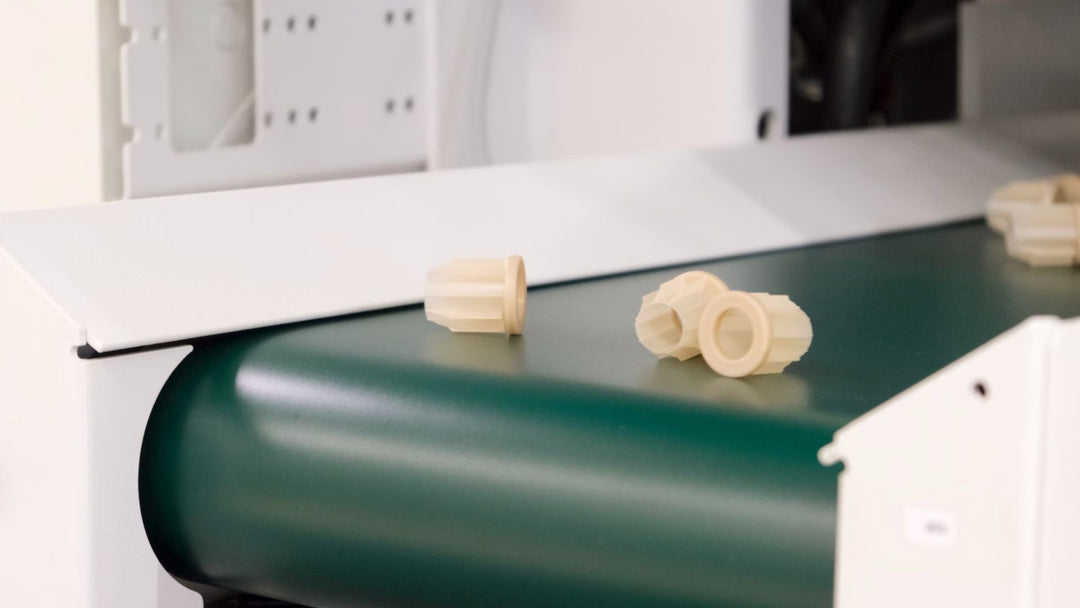